

.........pore to process integrated services..........
From reservoir to the process facility FLOPES will monitor your flow.
Some of our services include:
Core Services Description
Flow assurance studies
The key to the successful use of steady state and transient modelling is interpreting the results into a comprehensive operating strategy. Issues typically addressed are terrain induced slugging, hydrate, wax and asphaltene prevention and remediation, thermal control, production boosting, erosion or corrosion and complex rheology.From reservoir pore to the downstream facility, flow must be assured. However, for flow to be assured, transport energy driving the flow must overcome resistance to flow. With increasing water depth, technical and Flow Assurance challenge increases. This is primarily due to high pressure and low sea temperature. Onshore fields may also experience cold temperature related problems especially in harsh environments such as arctic circle. Increasing demand for oil and gas compels Exploration & Production companies to construct longer subsea lines in deeper water. This requires new technologies to monitor, operate and maintain production in more challenging environments.
Impediment to flow caused by either fluid phase behavior coupled with the dynamics of flow and or production-chemistry-related issues in the well bores and flow lines has long been identified in onshore or offshore shallow water environments. These events became more severe in deep water environment as the intervention is very challenging from technical and cost considerations. Naturally, these situations demand careful considerations of fluid phase behavior, fluid dynamics and production chemistry aspects at the design phase of field development.
Developing deep water fields requires substantial investment. The cost for a complete development can approach $4 billion. A deep water well can cost as much as $100 million to drill and complete. If well intervention, re-entry or work-over is required, day rates for rigs can cost $500 thousand /day. The high capital costs for deep water developments, the high intervention costs for remediating deep water systems, and the potential economic impacts of deferred production make the Flow Assurance strategy an essential centerpiece of field development plan. The goal of every Flow Assurance approach is to characterize and manage associated risks that can adversely affect hydrocarbon production. The main risks are from deposition of solids in the wellbore and flow lines due to gas hydrates, waxes, asphaltenes, mineral scale, and napthenates. Therefore, at floxpats, we focus on minimizing the risk of flow stoppage while transporting hydrocarbons from the pores of source rock to the destination facility.
Flow assurance services
FLOPES provides flow assurance engineering and consulting services for the Petroleum, Process Industry and nuclear industries on issues related to the hydraulic and thermal analysis of multiphase flow systems, transient flow modelling, 3-D flow simulations. Floxpat develops new solutions for the design and operation of multiphase production systems.Feasibility Studies
Multiphase flow
Multiphase flow activities range from basic research and laboratory experiments to design optimisation of multiphase components.FLOPES main activities with collaborating institutions:
Transient Multiphase Modelling
With the increasing flow assurance challenges encountered with deep water developments and long-range subsea tiebacks, transient multiphase flow simulation has become a standard technique for investigating system behaviour and operability.Steady State Thermal Hydraulic Modelling
Steady state modelling of multiphase well, pipeline and riser systems using advanced engineering tools in the market. FLOPES consultants are able to develop comprehensive and accurate models of converging, diverging and or looped production and injection systems including the selection of appropriate inflow performance relationships for modelling reservoir flows.Deliverability Modelling
Building a model from the reservoir to the facilities, we have looked at the effects of tubing and pipeline size, multiphase boosting, gas lift injection, subsea separation and various novel technologies such as hydrate slurry flow on the production rates achievable from a given configuration.Flow Splitter/Compact separation technology
From simple pipe arrangement to split incoming flow stream into liquid and gas to various destinations, compact separation technology is proving inevitable in hydrocarbon production. In some cases, flow splitter can be designed to be placed right at the bottom of the sea bed. Therefore, it is vital to get it right first time.
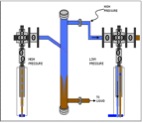
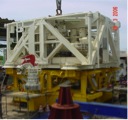
Gas Liquid Cylindrical Cyclone
Gas Liquid Cylindrical Cyclone application can be used as a wet gas scrubber to knock out the liquid droplets by modifying its configuration. For such application, it is crucial to understand the separation mechanism. The compact design can help debottleneck existing produced water treatment systems or increase capacity at relatively low cost. By splitting the multi-phase flow into its gas and liquid components, the individual phases are boosted separately, and finally co-mingled back into a single stream. This reduces the back pressure on wells, resulting in an increased volume of production.
Liquid loading in gas and gas condensate systems – Wet gas production and transportation
Prominently, the following flow patterns exist in multiphase flow systems: stratified flow, dispersed bubble, bubble, slug, churn and annular flow. Annular flow is the least understood of all these flow regimes. This is mainly due to its complex nature. Gas and gas condensate well and distribution networks operate in annular flow regime. Annular flow is characterized by a fast moving gas core with entrained liquid droplets and a slow moving liquid film flowing around the pipe wall. The film direction may be co-current or counter-current with the direction of the gas flow. The flow is associated with a wavy interfacial structure, which results in a high interfacial shear stress and pressure drop. Liquid loading into the gas well and in the gas condensate lines has been identified as a common problem that lowers productivity of gas well and in some cases can eventually kill the well before abandonment. The problem of liquid loading continues unabated due to lack of understanding of the mechanisms leading to liquid loading coupled with limited information about the atomization of part of the relatively slow moving liquid film by shear from the gas phase. The poor understanding of annular flow to various field and operational constraints where the atomization and entrainment of the liquid film imposes operational and performance limitations on various process and downstream equipment. At floxpat we have expert who can solve your liquid loading nightmare.
Training Courses
FLOPES offers a wide range of Flow Assurance courses that can be tailored to your particular needs and interests. Subjects include;For more information about our services, please send us email : info@floxpat.com